Laser Cutting
Have you ever bought a shoe and it was just the wrong size? This week I was trying to solve this problem. I am laser cutting a modular parametric shoe. This shoe will be printed in pieces which can be assembled together for the best fit. This idea when combined with the vinyl cutting assignment can give you access to any shoe brand: Nike, Adidas, New Balence etc.
1. Parameterizing
This took much longer than I expected because of my unfamilarity with Fusion 360. In the beginning of the week instead of planning out the shapes I was just drawing willy nilly. I was using parameters but everytime I change the parameters the shapes would not grow rather they would get deformed.
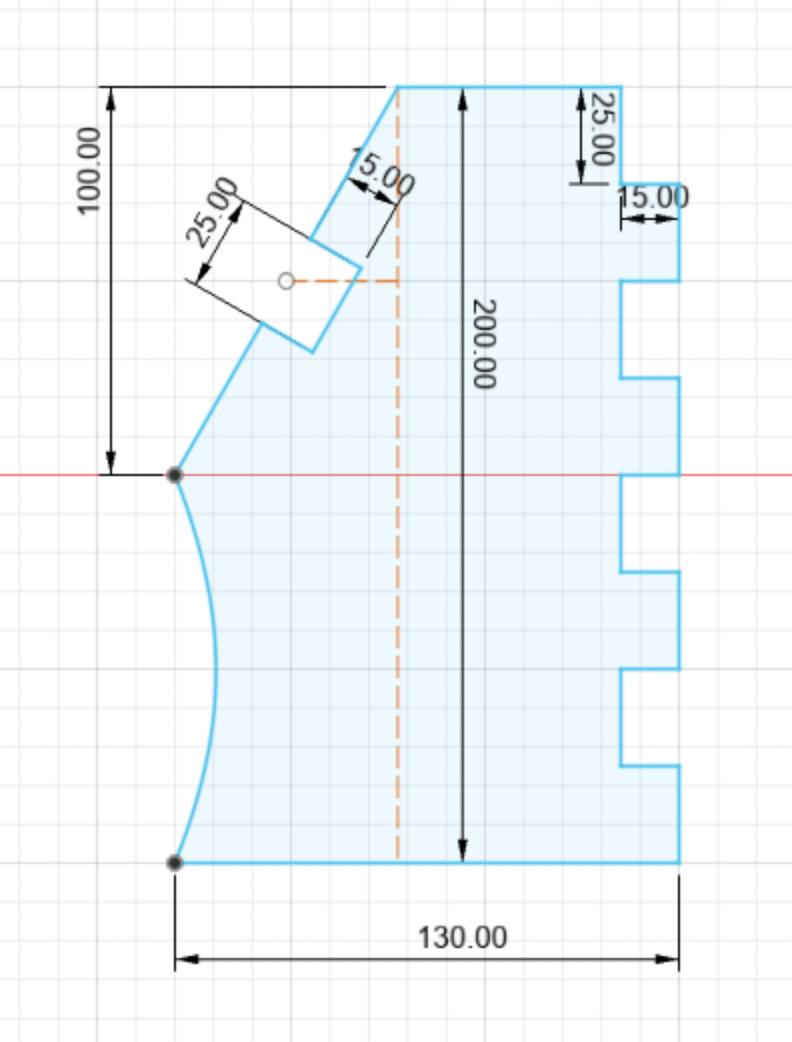
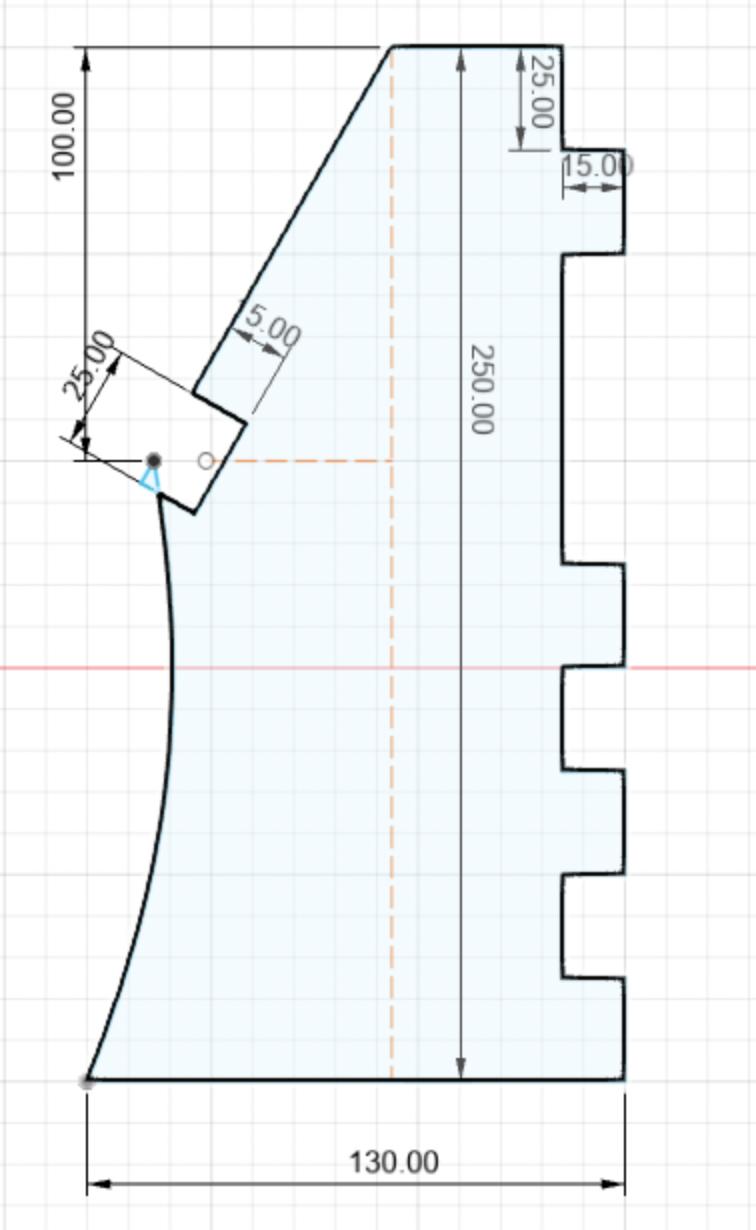
This caused many problems, when I made small mistakes and tried to fix them I eneded up having to remake the entire shape. Because of this I made too many designs. Although this did help me understand Fusion a little better. Each iteration I learned how to add shapes a little bit better. Specifically rectangles which I was using as holes for other peices to go into caused me some major problems. At first, I was drawing each rectable by "hand".
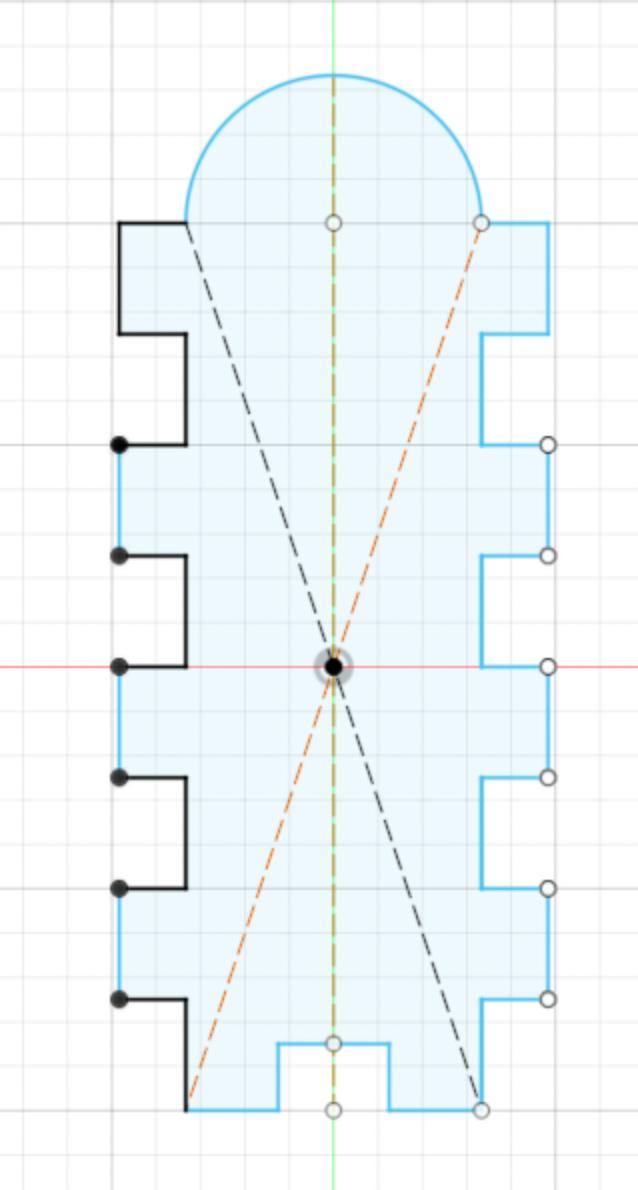
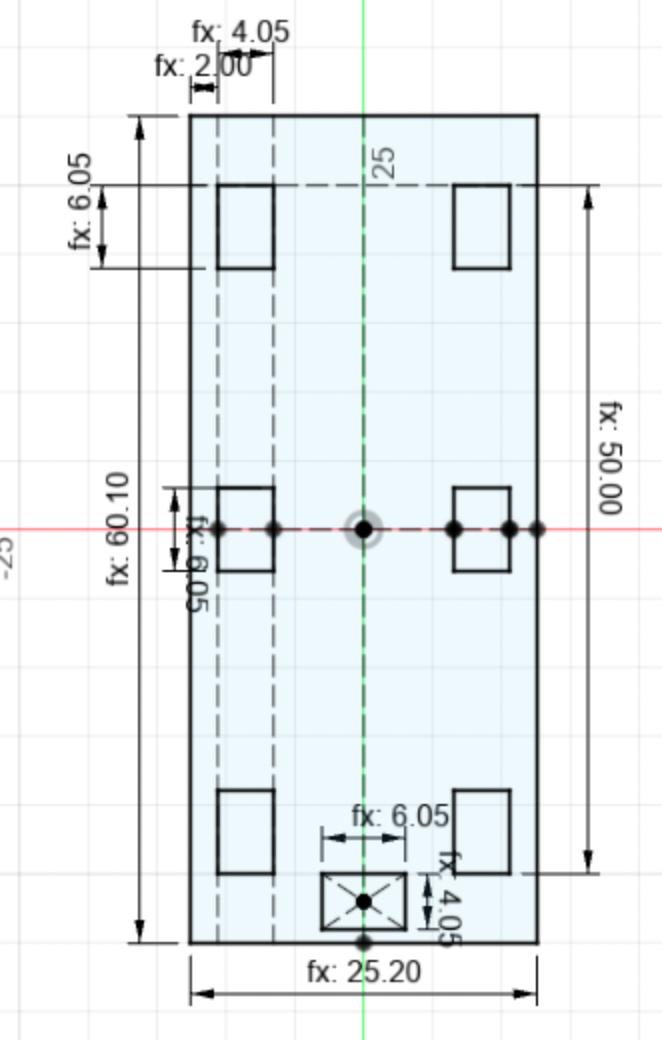
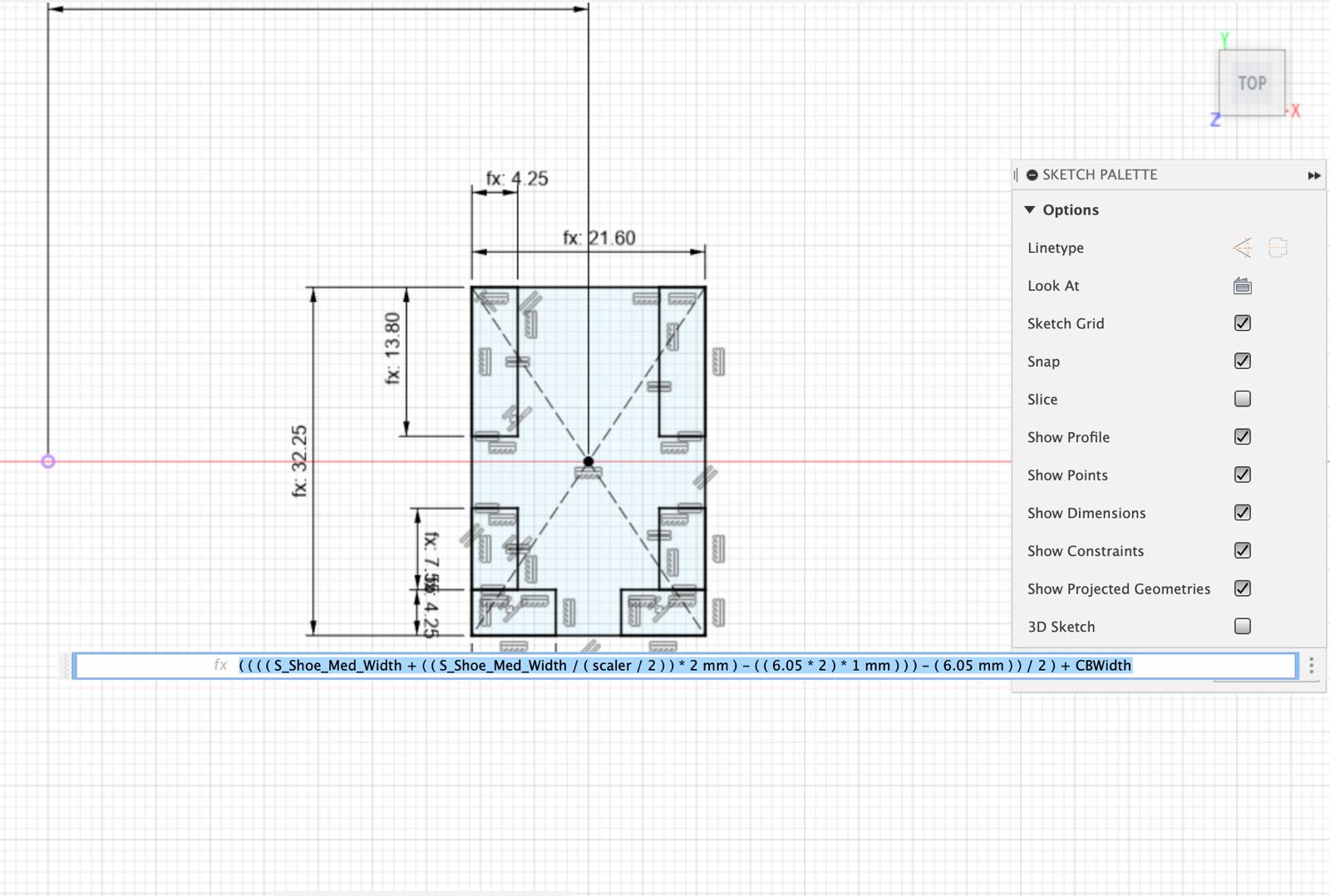
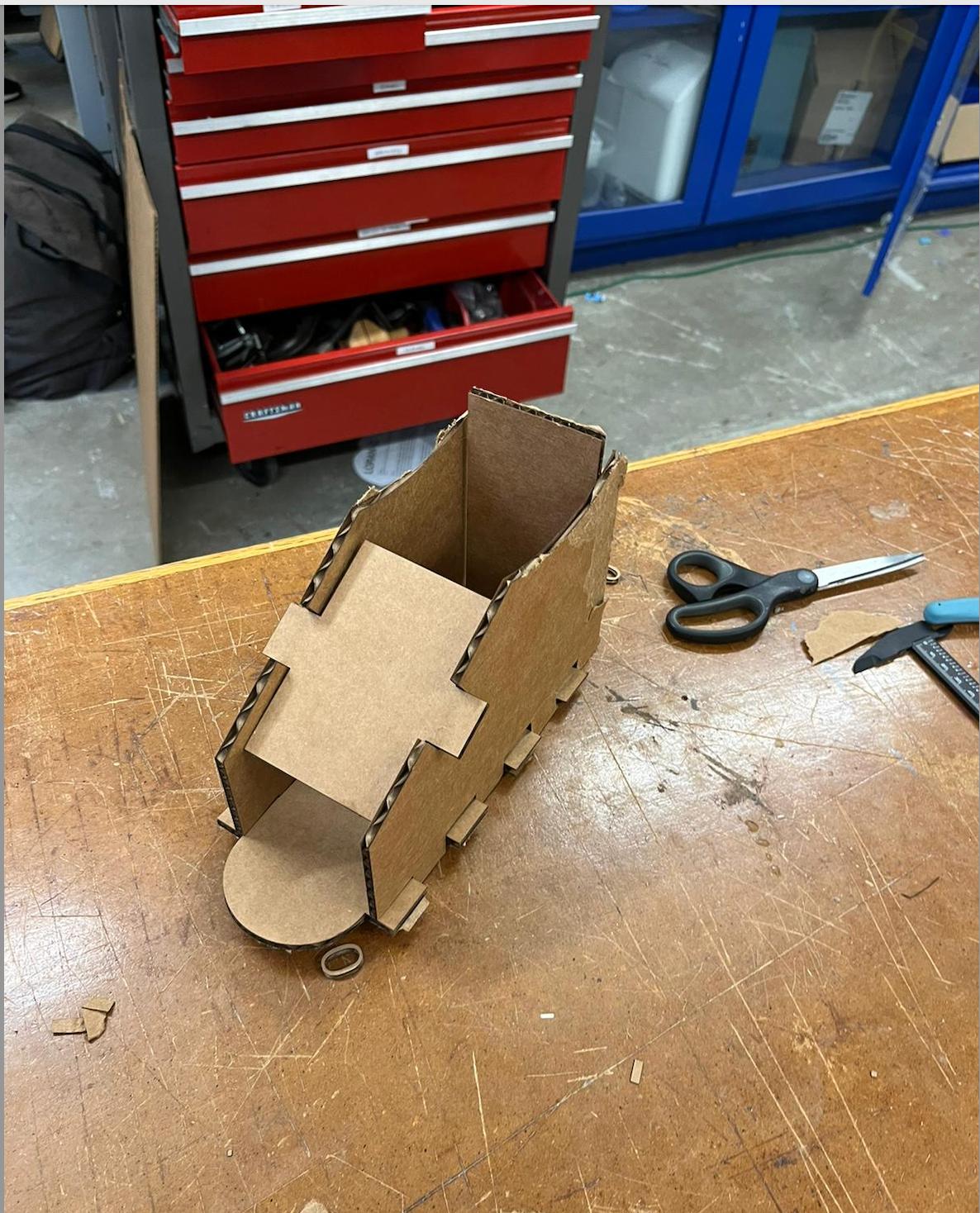
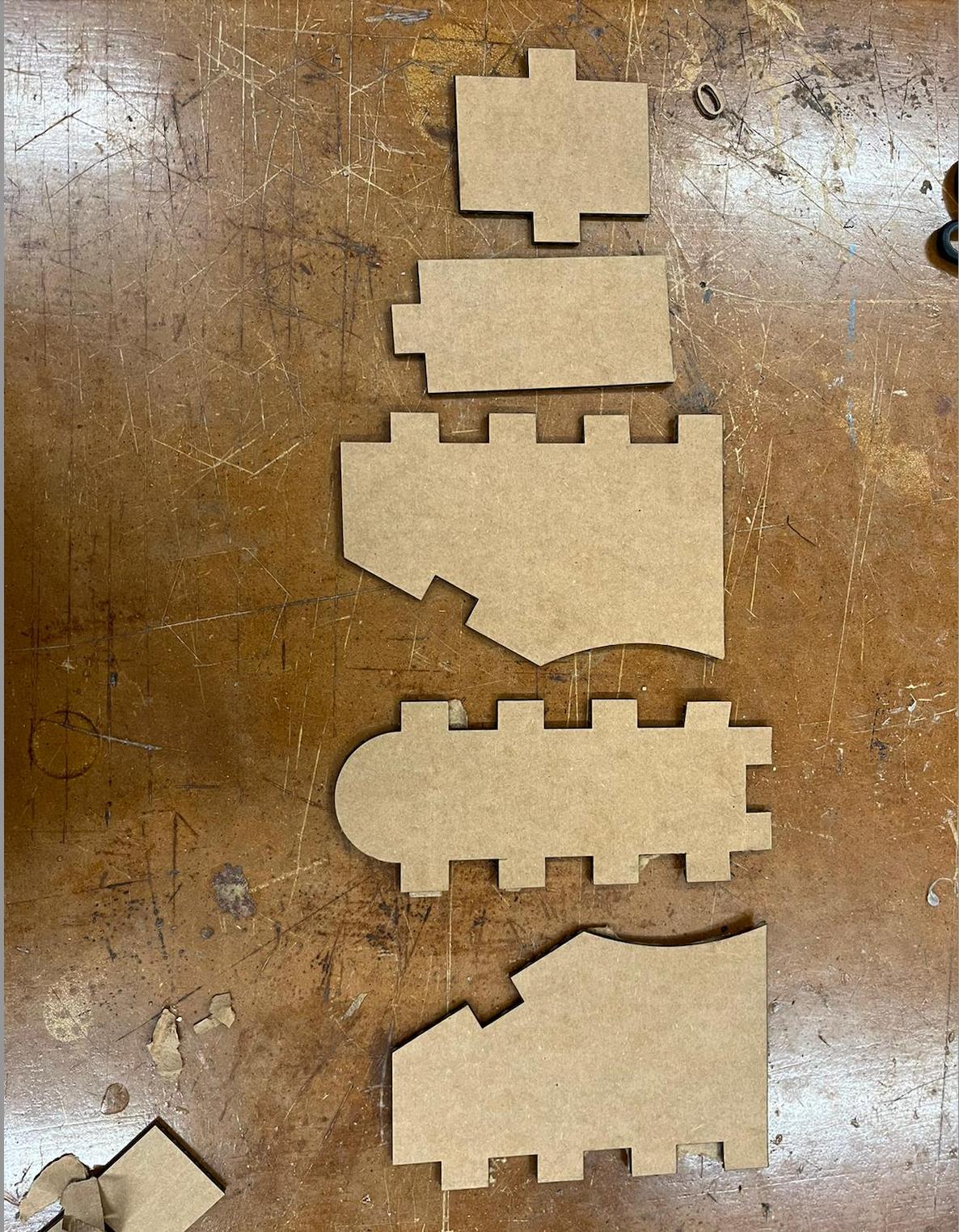
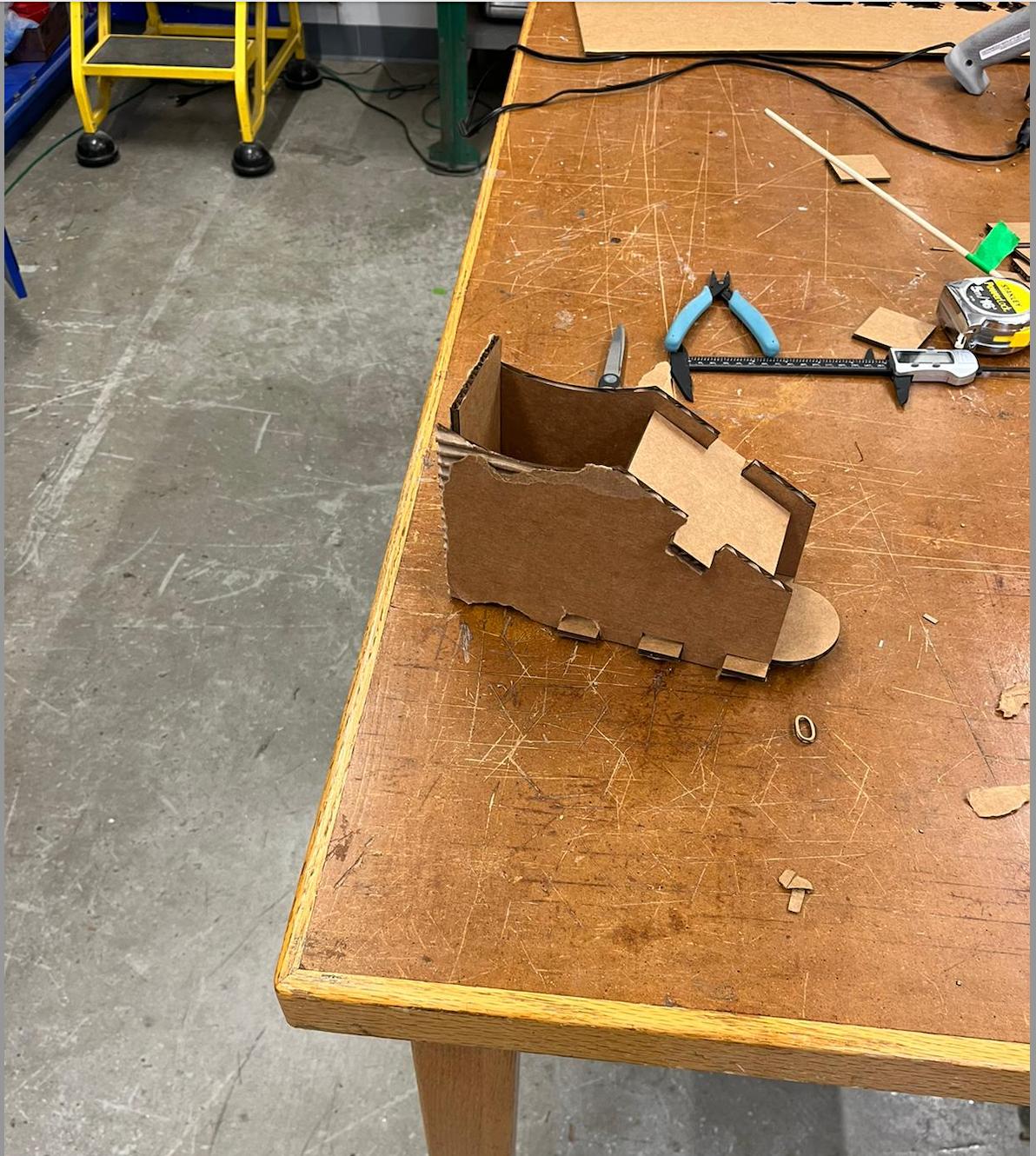
2. The dreaded blue lines
I orginally did not understand the concept of constraints. I could not grasp that there is a chance that my constrains could in a way which does not completely constrain the image. These signs meant nothing to me.
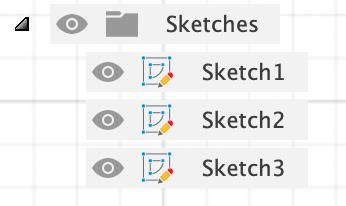
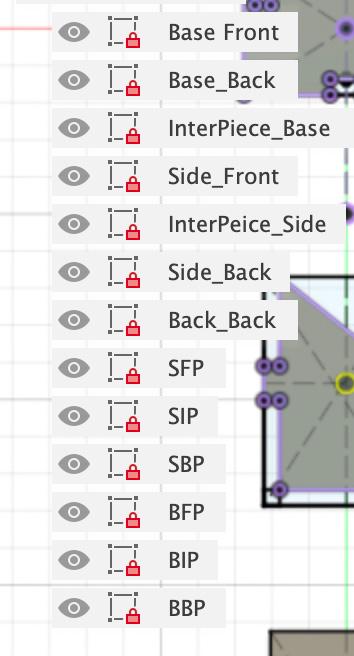
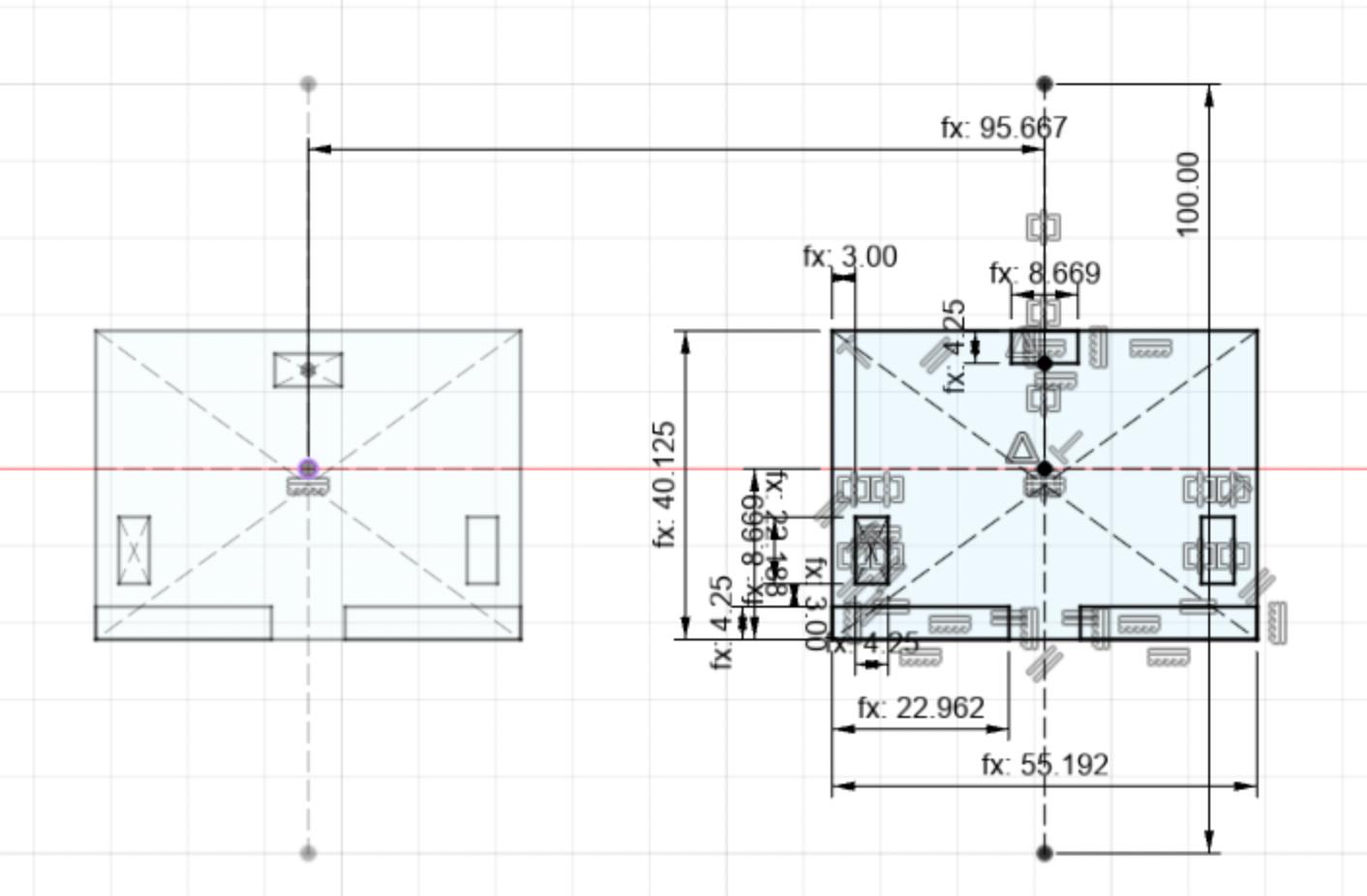
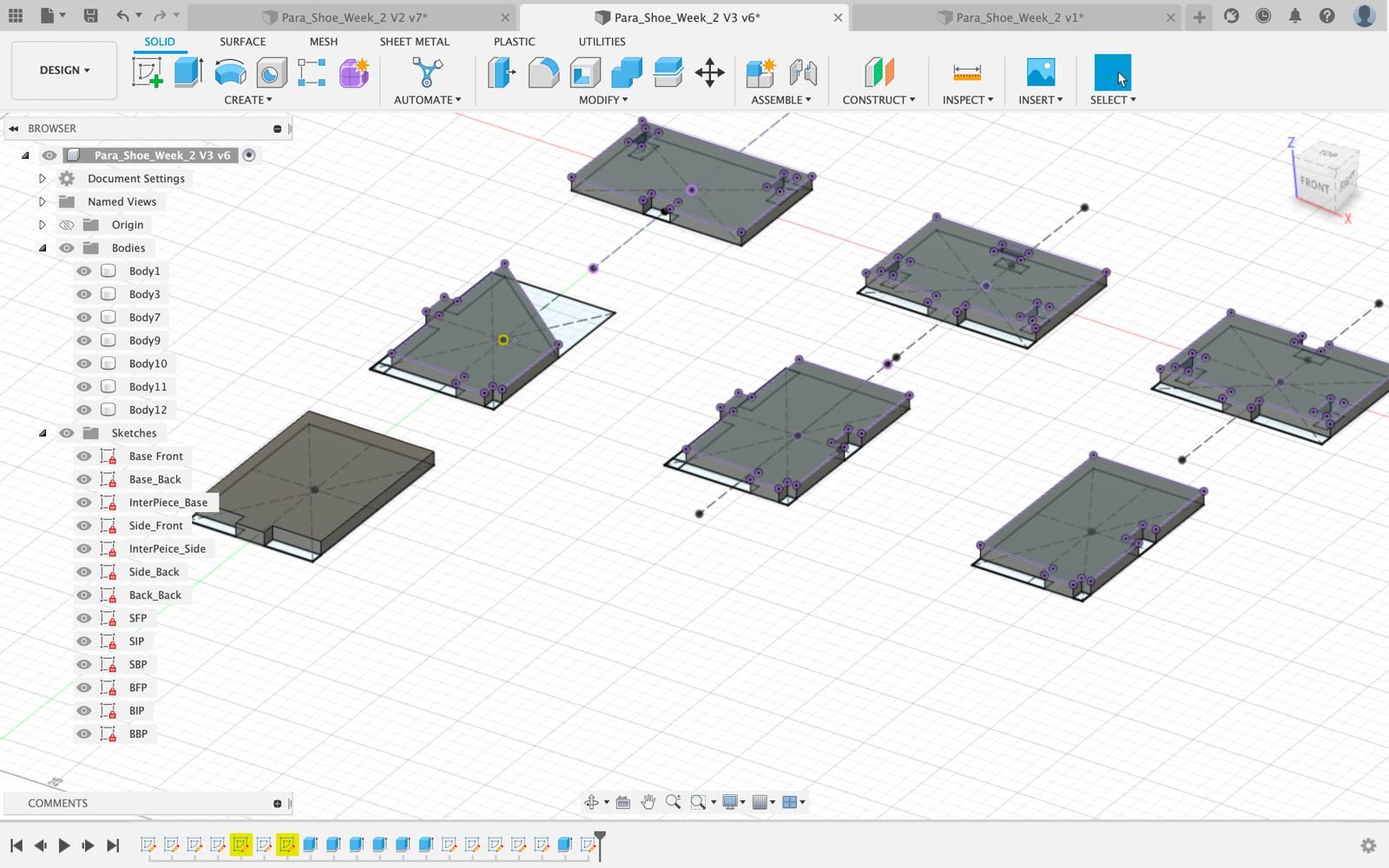
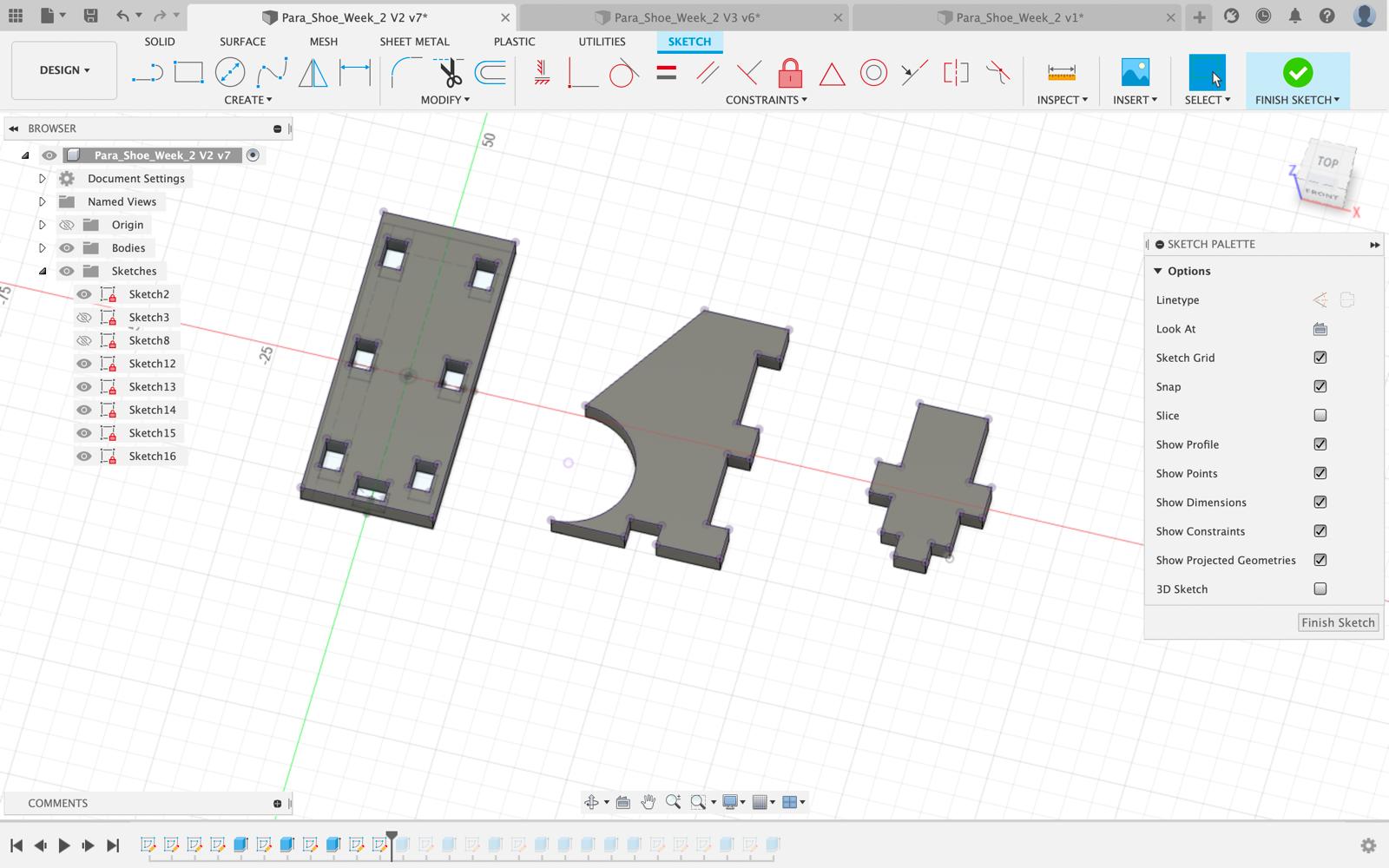
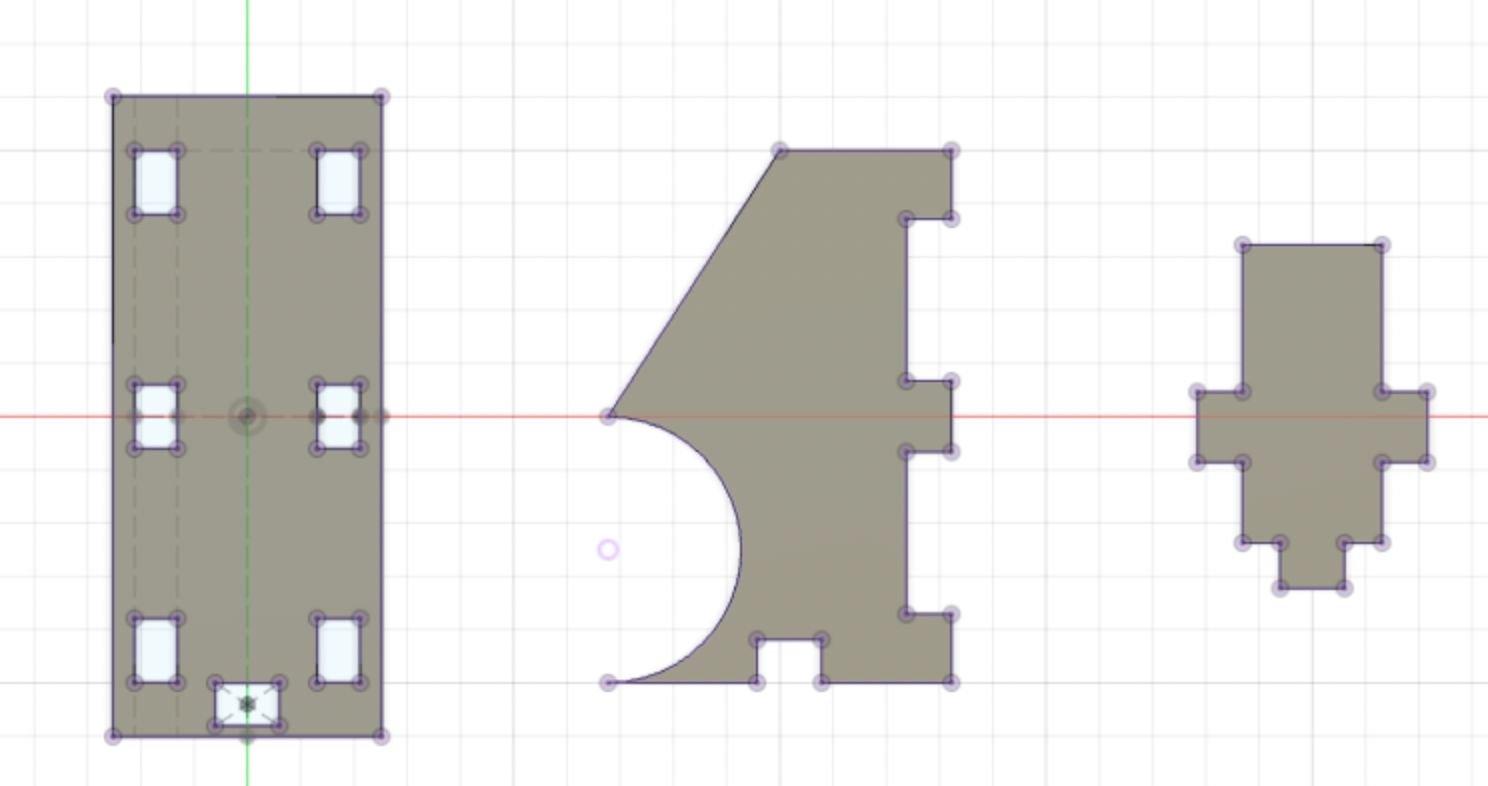
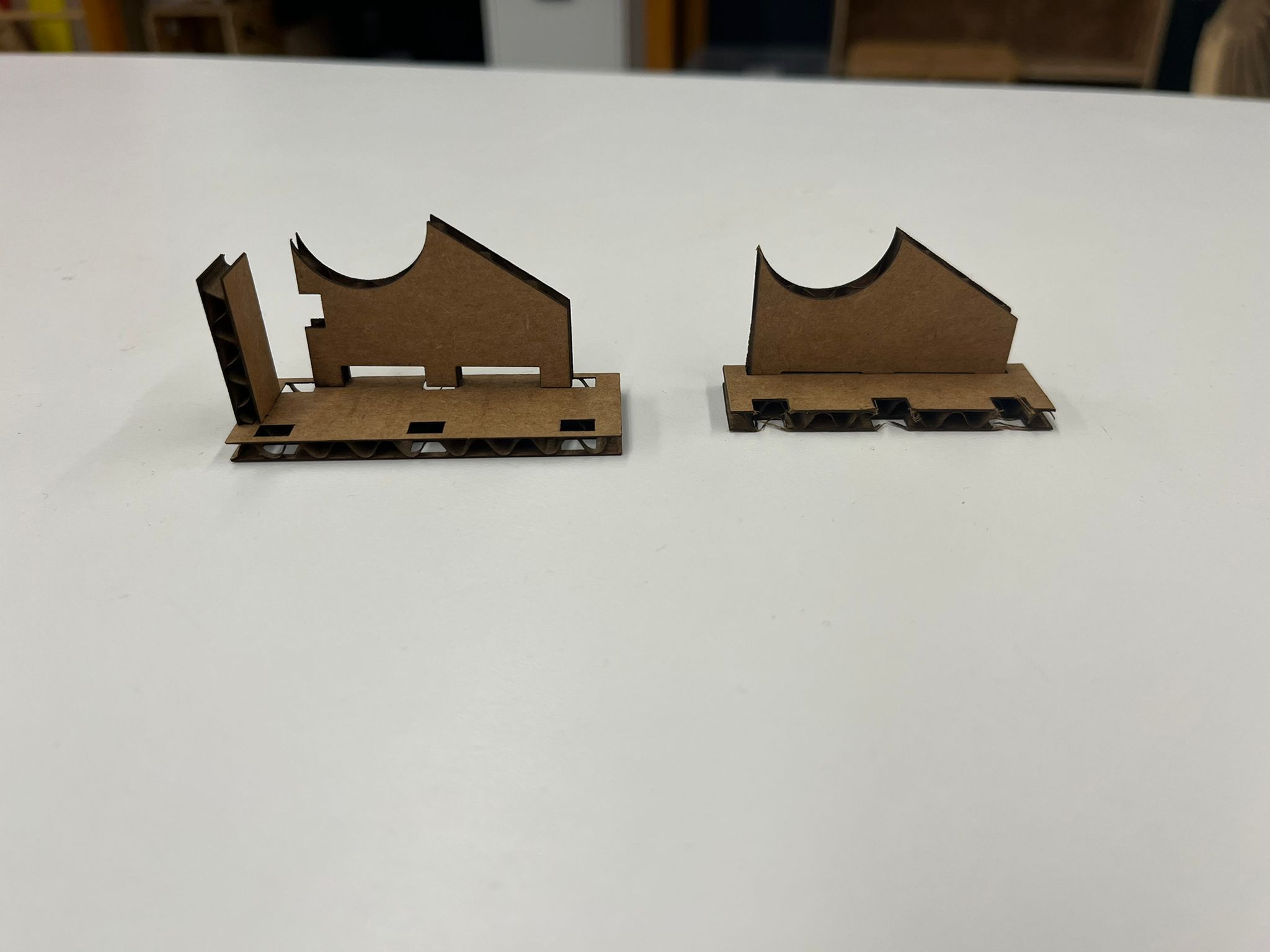
3. Modulizing
The last step in the process was to make the shoes modular. In order to do that I turned each of the components, the base side and back into parts that can be fit together. I made a front a back and an inbetween piece for the base and sides.
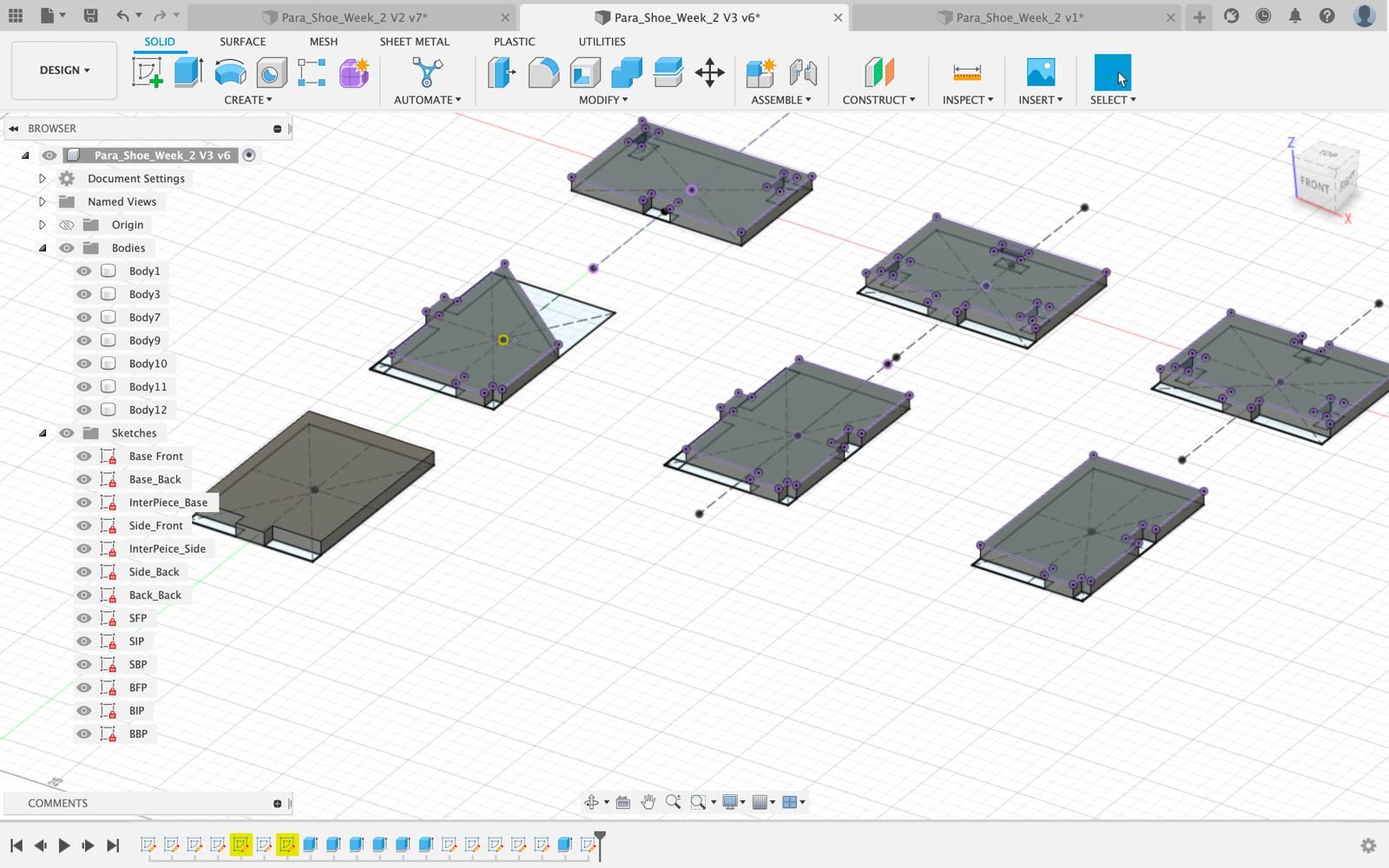
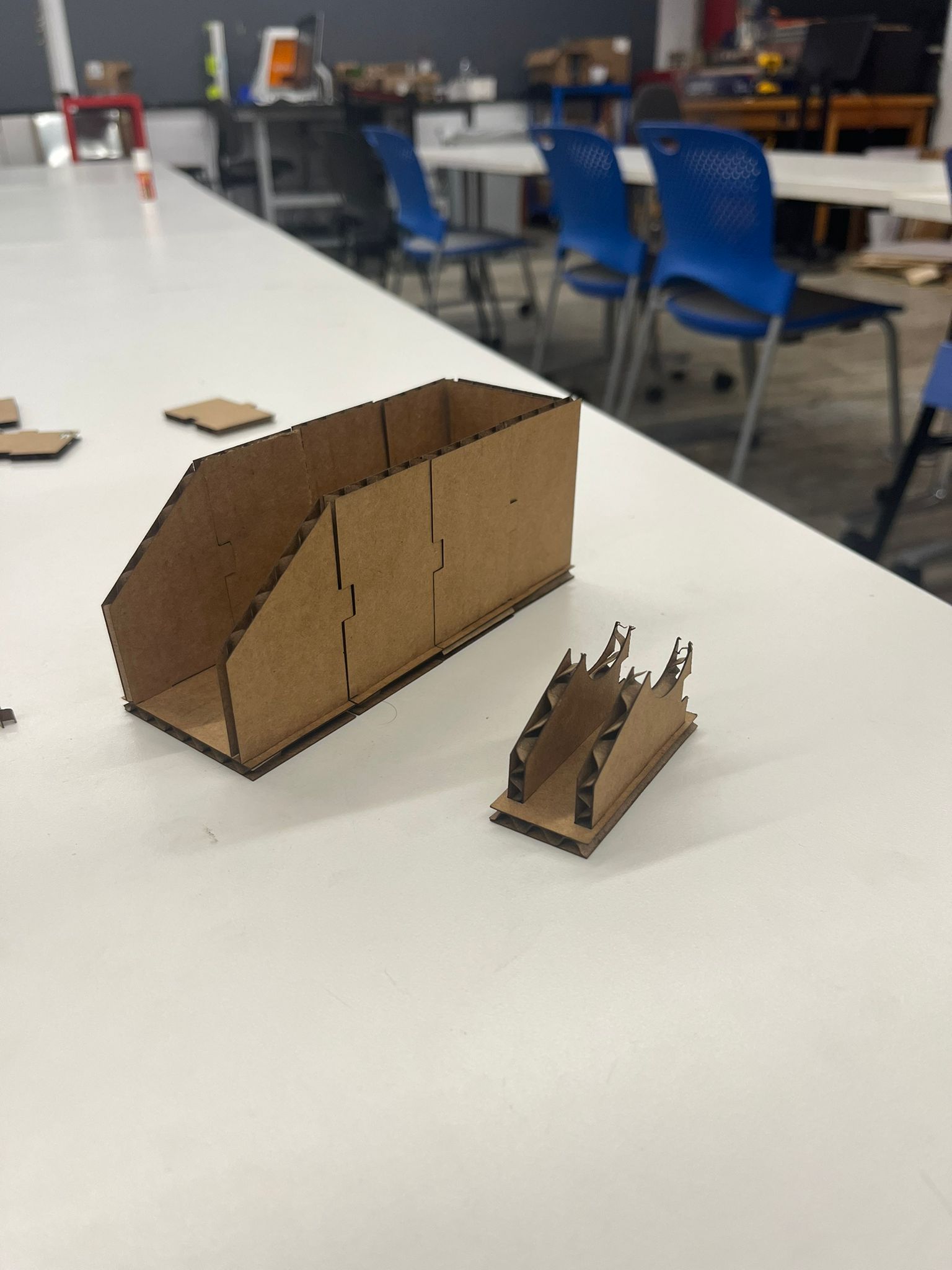
Vinyle Cutting
Using the vinyle cutter at Harvard was suprisingly easy when it was working. All I had to do was upload a png and it was able to cute very well once I figured out the force. For this week I was cutting out sneaker brand logos.
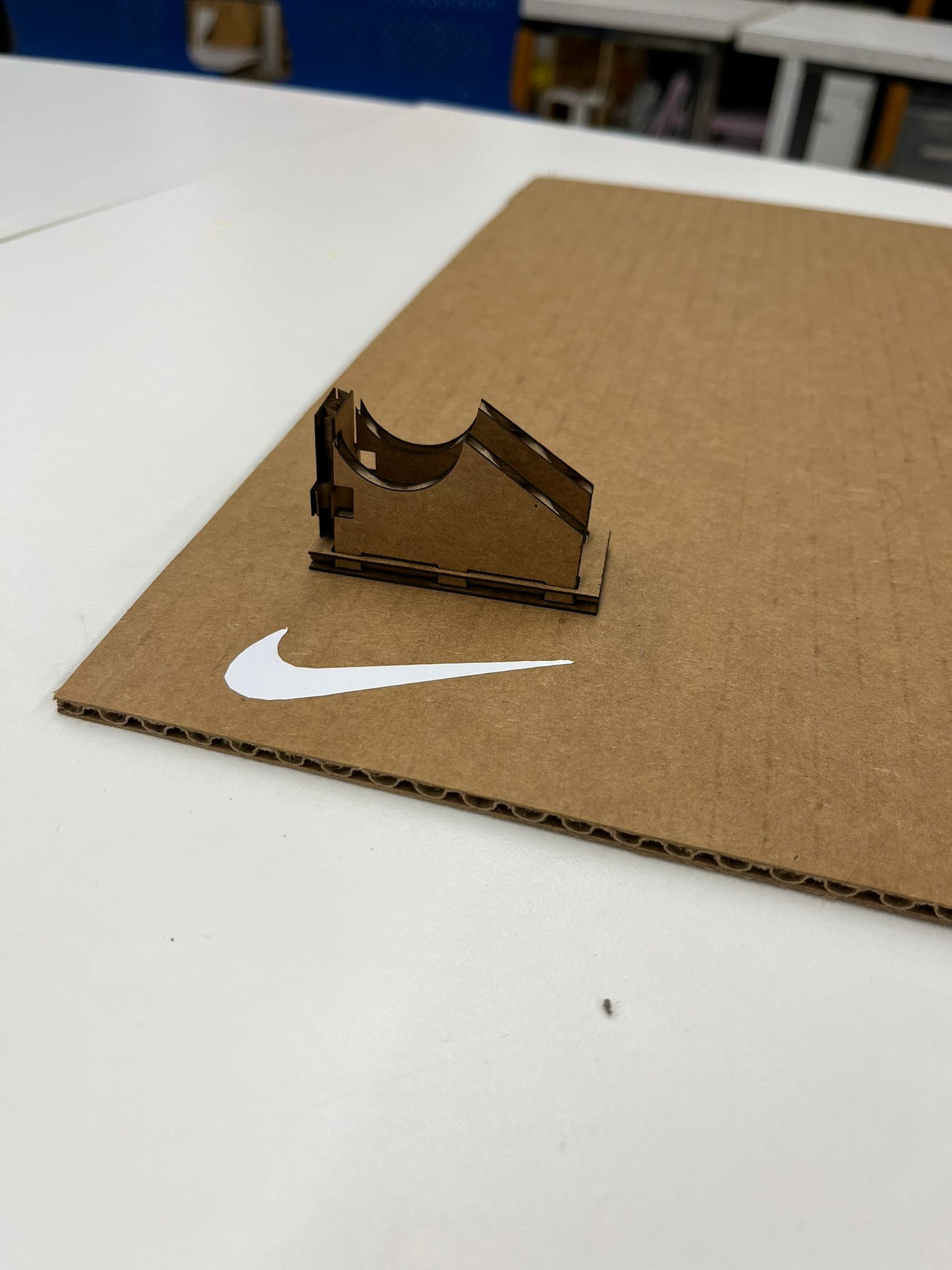
Unforseen Problem
Although both the laser cutting and vinyle cutting went really fast the machines had lines to use them. Specifically the laser cutter was not cutting well no matter the power or speed, so it would take people really long to cut everything they wanted. The vinyle cutter was causing problems because the computer just stopped reading the vinyle cutter.